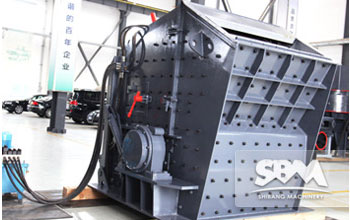
Analysis Of Materials For Wear-Resistant Parts
Impact crusher is a kind of very important secondary crushing equipment used in crushing plants. As we know, impact crusher crushes raw materials through the impact force produced by high-speed blow bar, and shoots them on the impact plate.
From this we can see that, the main wear-resistant parts in impact crusher are blow bar and impact plate. In this article, we focus on analysis of materials for making wear-resistant parts in impact crusher.
Analysis Of Materials For Wear-Resistant Parts
Operating Condition
In the operating process of impact crusher, the above mentioned wear-resistant parts are under great impact force. Besides, the high-speed blow bar and the raw materials collide again and again, leading to the surface temperature of blow bar increasing rapidly and reaching to very high degree. So the materials to make wear-resistant parts should have enough hardness and toughness in high temperature.
Abrasion Mechanism
The abrasion mechanism of blow bar, impact plate is mainly gouging abrasion, which is a kind of groove abrasion with relatively strong surface strain and mechanical strain. The groove forms because that raw materials cut in the metallic material under effect of external force. After a length of sliding, raw materials will separate the parts and there will be groove on the surface of the wear-resistant parts.
Material Selection
According to the working principle of impact crusher and the abrasion mechanism, we can see that the material selected should have proper hardness and toughness. So the manufacturing of the material should be paid special attention.
Casting technique: the selected high chrome alloyed cast iron contains much alloy; it features good flowability and large shrinkage and poor conductivity, so while designing its casting technique, manufacturers should adopt progressive solidification and strengthen the feeding effect.
Heat treatment: the heat treatment should include quenching and tempering. Besides, in the heat treatment process, manufacturers should eliminate the heat treatment of stress to avoid part in the early stage.
Get Price And Support
Simply complete the form below, click submit, you will get the price list and a SBM representative will contact you within one business day. Please also feel free to contact us by email or phone. ( * Denotes a required field).